8層への挑戦
クリップボードにコピーしました
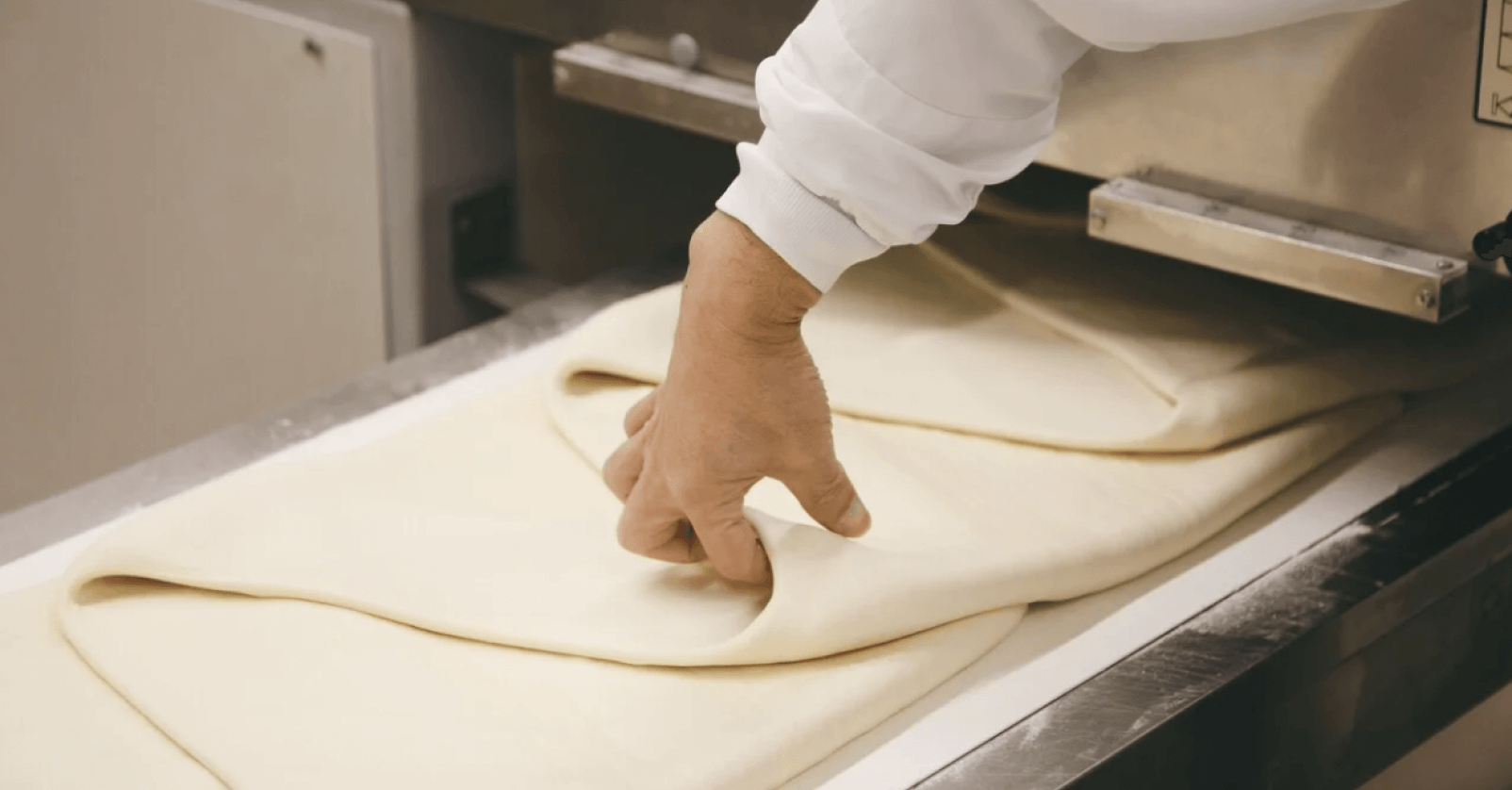
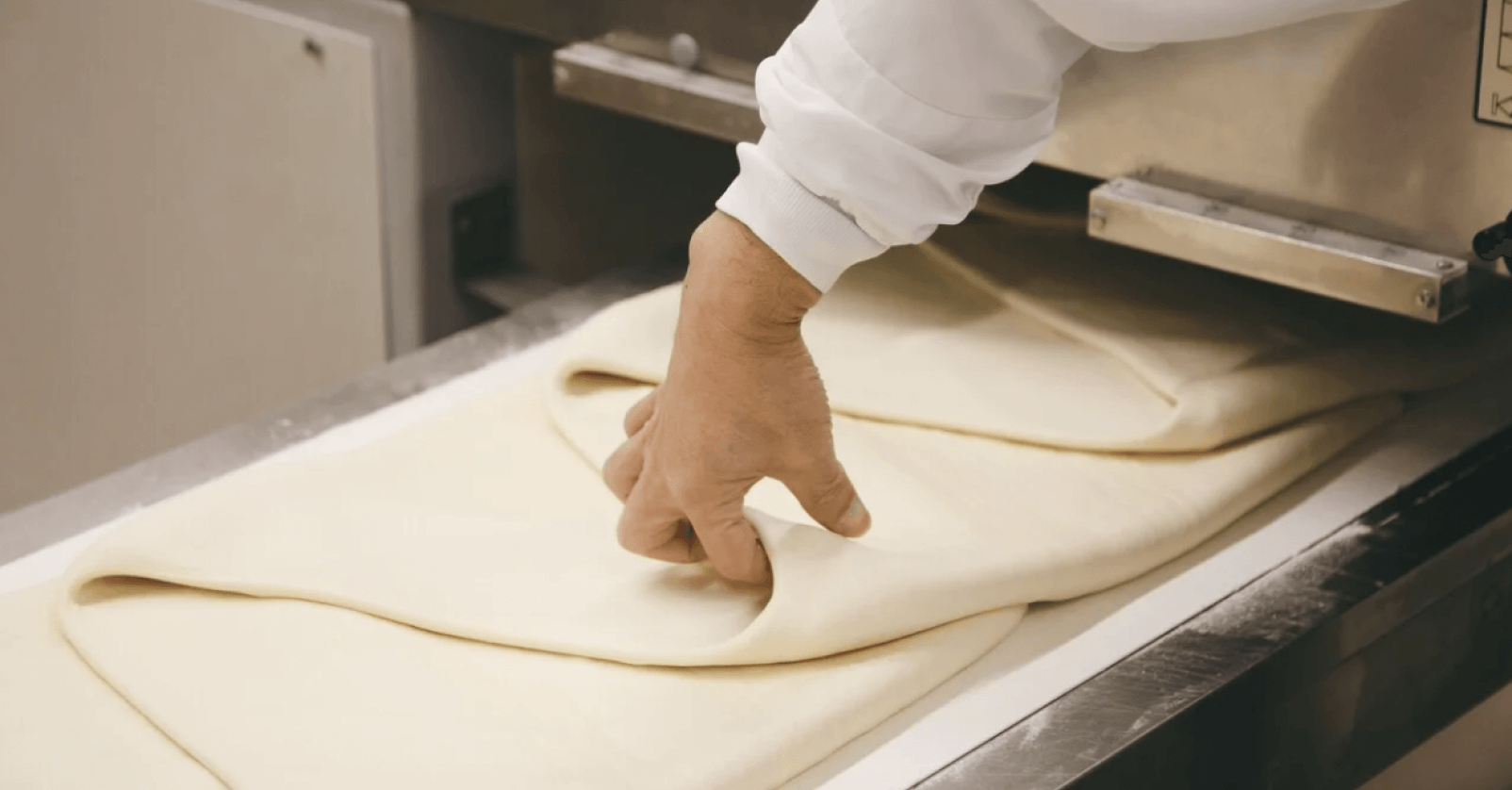
アメリカでは、1940年代に深夜・早朝・休日作業を廃止すべく製パン工程の見直しが行なわれ、短時間製パン法やノータイム法など様々な方法が開発された。1970年代には日本にもこれらの方法が紹介されたが、従来のパンと比べて味が落ちるとされ、普及には至らなかった。
冷凍生地による製パンの研究が行われるようになったのはこの頃だ。日本ではベーカリーレストランの「アンデルセン」が国内初の冷凍パン工場を設立し、1980年代には冷凍生地を使った焼き立てパンを提供するオーブンフレッシュベーカリーが全国各地に増加した。
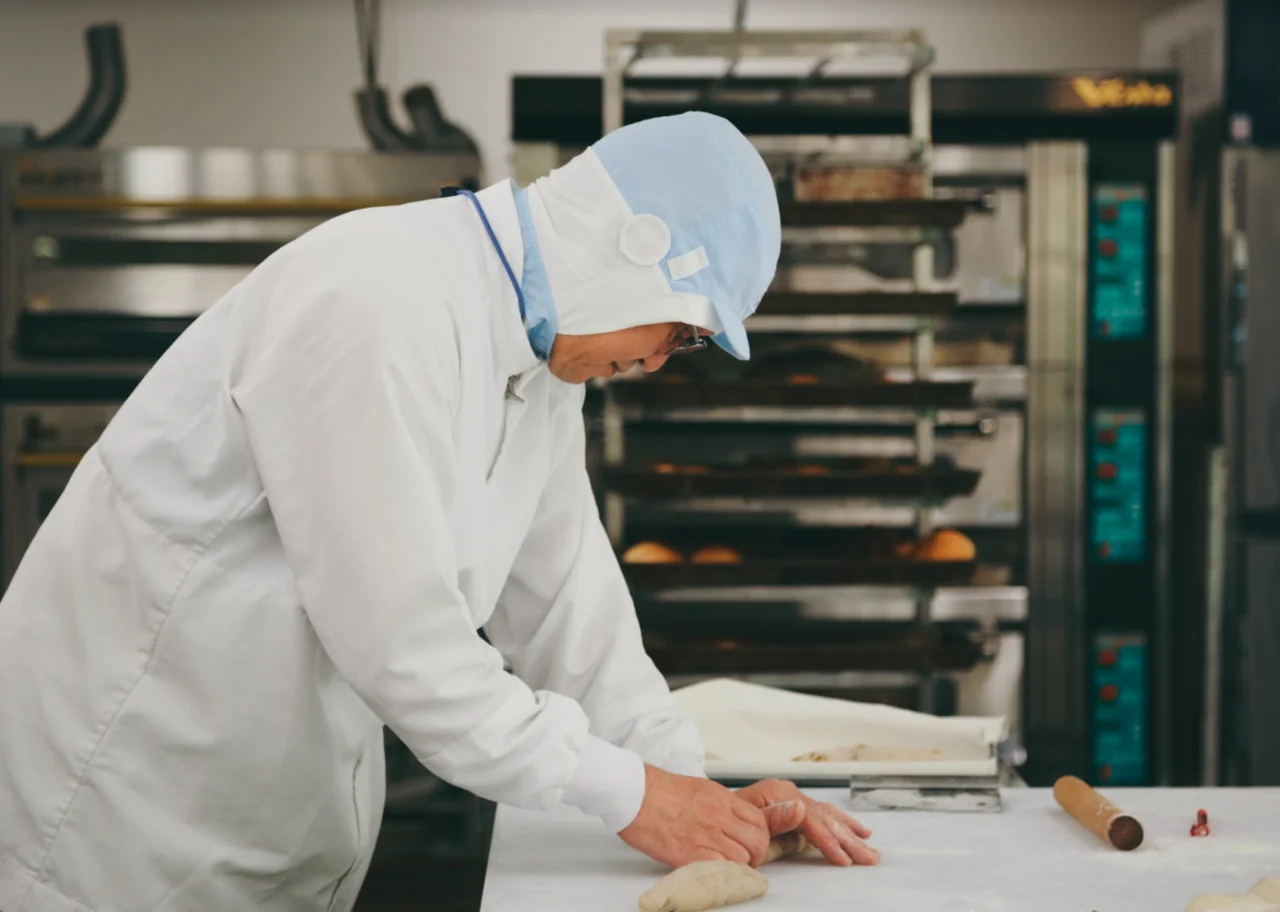
大阪で小麦粉をはじめとする製パン材料の卸売をしていた勇商店(のちのイズム)が、冷凍生地製造を始めたのもちょうどこの頃。当時から現在まで、30年以上にわたって様々な製品開発に携わってきた「イズム研究開発部」の田部井氏は言う。
田部井「冷凍生地の立ち位置もだいぶ変わりました。昔と違って、今は焼き立てよりもシェフの個性が求められる時代。私たちがやるべきことも徐々に変わってきていると感じます」
思い込みからの脱却
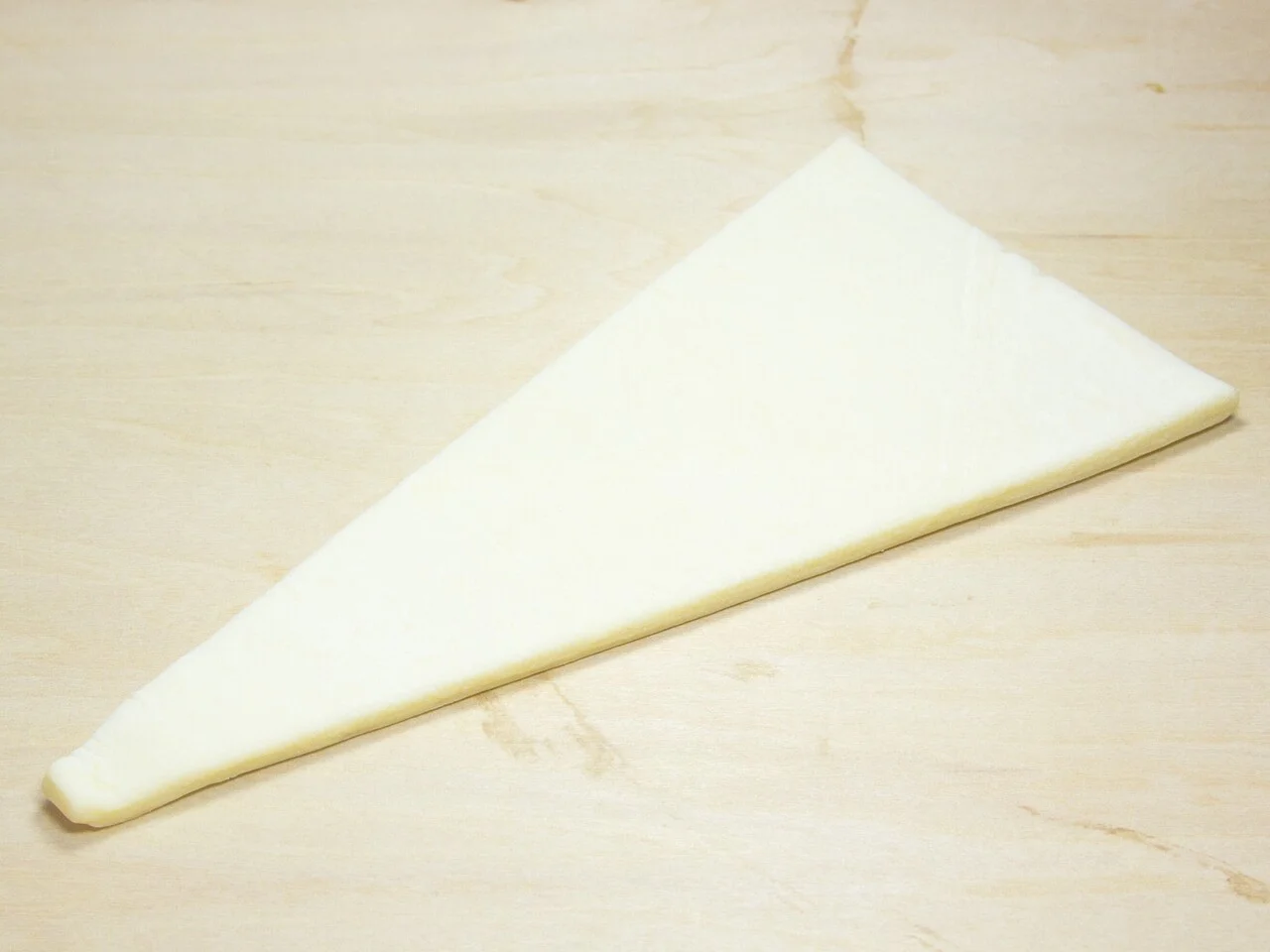
イズムが8層のクロワッサン生地を開発したのはおよそ2年前。
当時、巷では、ある有名店が考案した9層のクロワッサンをきっかけに、層の少ないクロワッサンへの注目が集まっていた。スタンダードと言われる27層よりもザクザクの食感で、バターの香りがよりダイレクトに感じられる9層のクロワッサンは、多くの消費者の支持を集めたのだ。
ブームが続くなか、イズムにも「冷凍生地で層の少ないクロワッサンがつくれないか」とシェフたちからリクエストが届き始める。
田部井「はじめのうちはお断りしていたんです。機械の構造上、私たちにできるのは 16層が最低ラインというのが当時の認識でした。工場では練った生地と油脂のシートを重ねた状態で蛇腹折りにしながらズラし、それを上からプレスして層をつくる方法を採用しています。蛇腹の数はベルトコンベアのスピードで調整ができますが、この時に できる折の最小単位が「4」 だと思っていたんです。この工程は2つのラインで1回ずつ行われるので、4つ折2回(4×4)で16層。あとは6つ折と8つ折を組み合わせながら目指す食感にあわせて折り層を増やすことができますが、減らすという発想はなかった。とにかくそういうものなんだと、当時はなんの疑いもありませんでした」(写真:6つ折の製造工程)

しかし断ったものの、「頭の片隅ではこの時のことがずっと気がかりだった」という田部井氏。
田部井「理論上はもしかすると可能なんじゃないか…という気持ちもありました。そもそもクロワッサンやパイのようにバターの層があるパンは、層が多ければ多いほど一枚一枚の生地が薄くなって軽いパンができます。それはそれで良いのですが、機械でつくる場合は機械自体が生地にできるだけストレスをかけないような造りになっているので、 人の手でつくる生地と比べて弾力がどうしても弱くなってしまう んです。人の手でつくるのと同じような配合で同じようなことをしていても、機械でつくったものは軽さがやや出すぎる。もっと食感のある香り高いクロワッサンをつくりたい、というのは私たちが以前から目指していたことでもありました」
可能性を信じた開発部は、それまでの最小単位と考えていた「4つ折2回」を打ち破るべく検証を開始。試行錯誤を続けていくなかである日ふと、 一方のベルトコンベアを通常より速く動かせば1回あたりの折数を2(通常の1/2)に減らせる ことに気がつく。
田部井「まさに盲点でした。『そもそもなんでできないんだっけ』と自問自答して考え続けているうちにふっと降りてきたんですよね。裏を返せば、すごくシンプルなことなのにそれまで全く思いもしなかった。考えようとしなければ気づけないものなんだな、と」
機械を何度も調整し、綺麗な2つ折をつくるための数値を算出。2つ折のラインと通常の4つ折ラインを組み合わせれば、これで念願の8層ができる…わけではなかった。
閃きを掴んだ指先
製造部協力のもと2つ折を実装させてみると、新たな課題が浮上した。生地が欠けてしまったり、切れてバラバラになってしまったりと、クロワッサン生地と言うには遠く及ばないものが出来てしまったのだ。
機械に不具合はない。数値的にも間違っていないはず。ではなぜうまくいかなかったのか?
田部井「生地の状態って、本当にちょっとしたことで変わっていきます。特に温度変化から受ける影響っていうのはすごくシビアで、 練り上がった生地自体の温度はもちろん、その日の室温でも 全然違ってきます。その様子を逐一把握して、生地の状態にあわせて機械も微調整を行わないと、結局失敗するんですよね。手前の工程での仕上がり状況も常に気にしながら、目の前の生地に合った対応をとっていかないといけないんです」
製造部のメンバーはそれぞれの経験と知識、目と指先の感覚を活かして、開発部のアイデアを実現すべくチャレンジを継続。そうするうちに、一人また一人と機械と生地の感覚を掴み、遂に綺麗な2つ折が実現した。
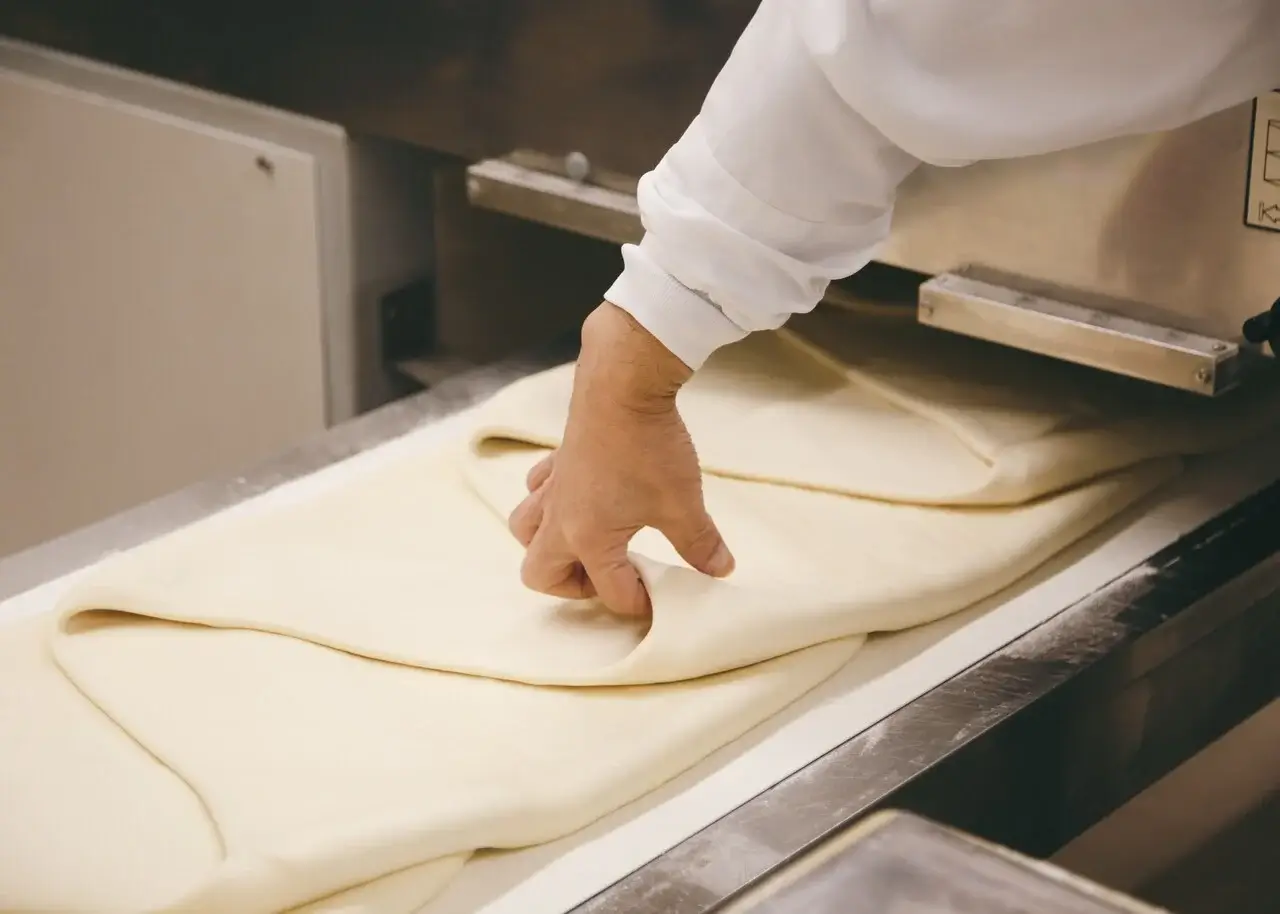
田部井「チーム全体のスキルとして確立するまでには少し時間がかかりましたが、コツを掴んだメンバーの助言を受けながら他のメンバーも徐々に自分のものにしていってくれました。彼らを見ていると、職人だなと思いますね。機械のことをよくよく理解する製造部がいるからこそ、開発を行う私たちも挑み続けられるんです」
そうして完成したクロワッサン生地には、「ISMのこだわりクロワッサン板50」という名前がつけられた。
ヒントはパン屋の厨房
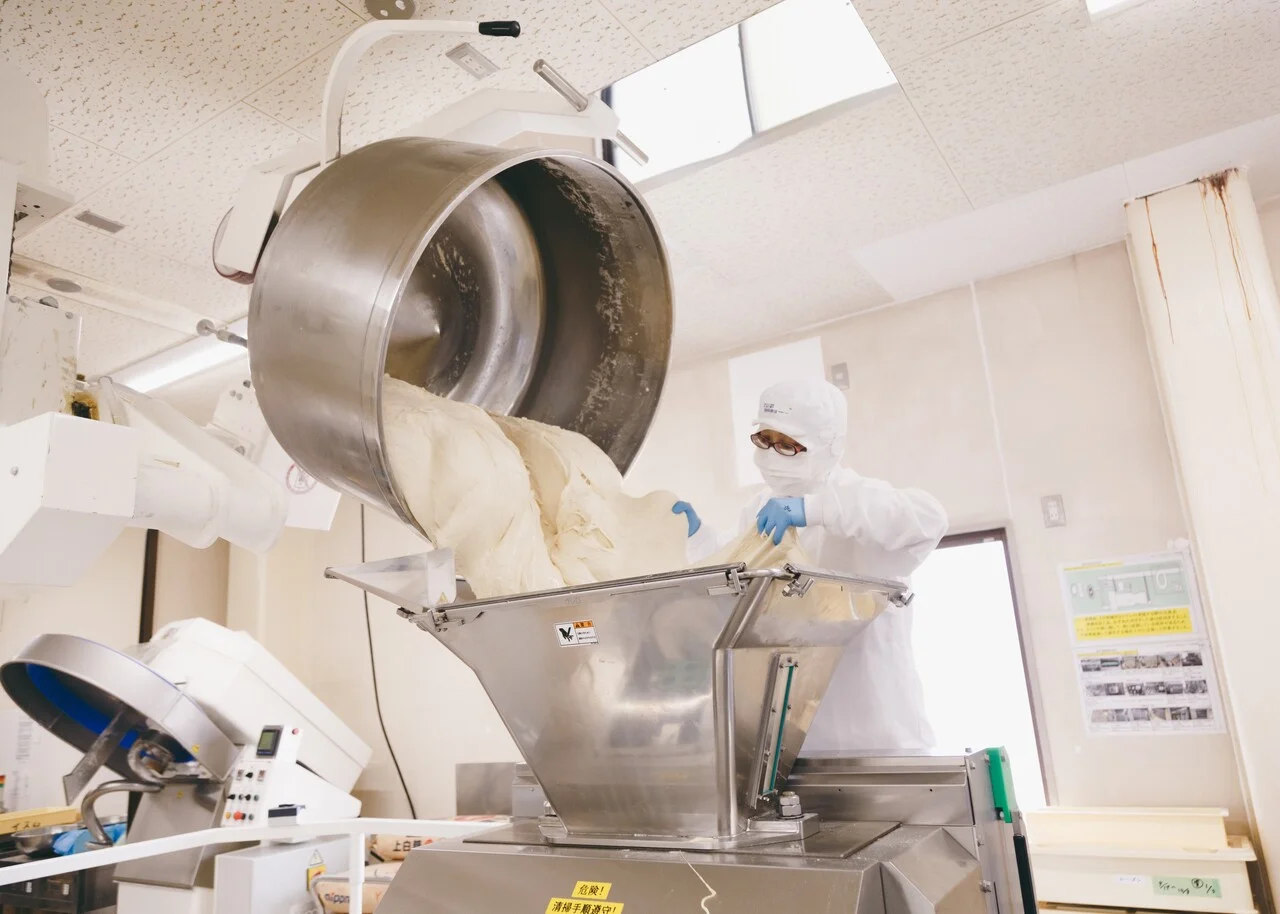
イズムの原点である大阪・四條畷(しじょうなわて)の工場には、製パンの現場に基づく様々なアイデアが詰まっている。
その象徴とも言えるのが、分断された油脂の折込ラインだ。
イズムの工場では、一度目の折込が終わると一旦生地をカットし、ラインから下ろす作業を行う。二度目の折込の際は別のラインへと移され、生地をもう一度ラインに置いて生地を繋ぎ直す。(写真上:一度目の折込ライン終着点/下:二度目の折込ラインスタート地点)
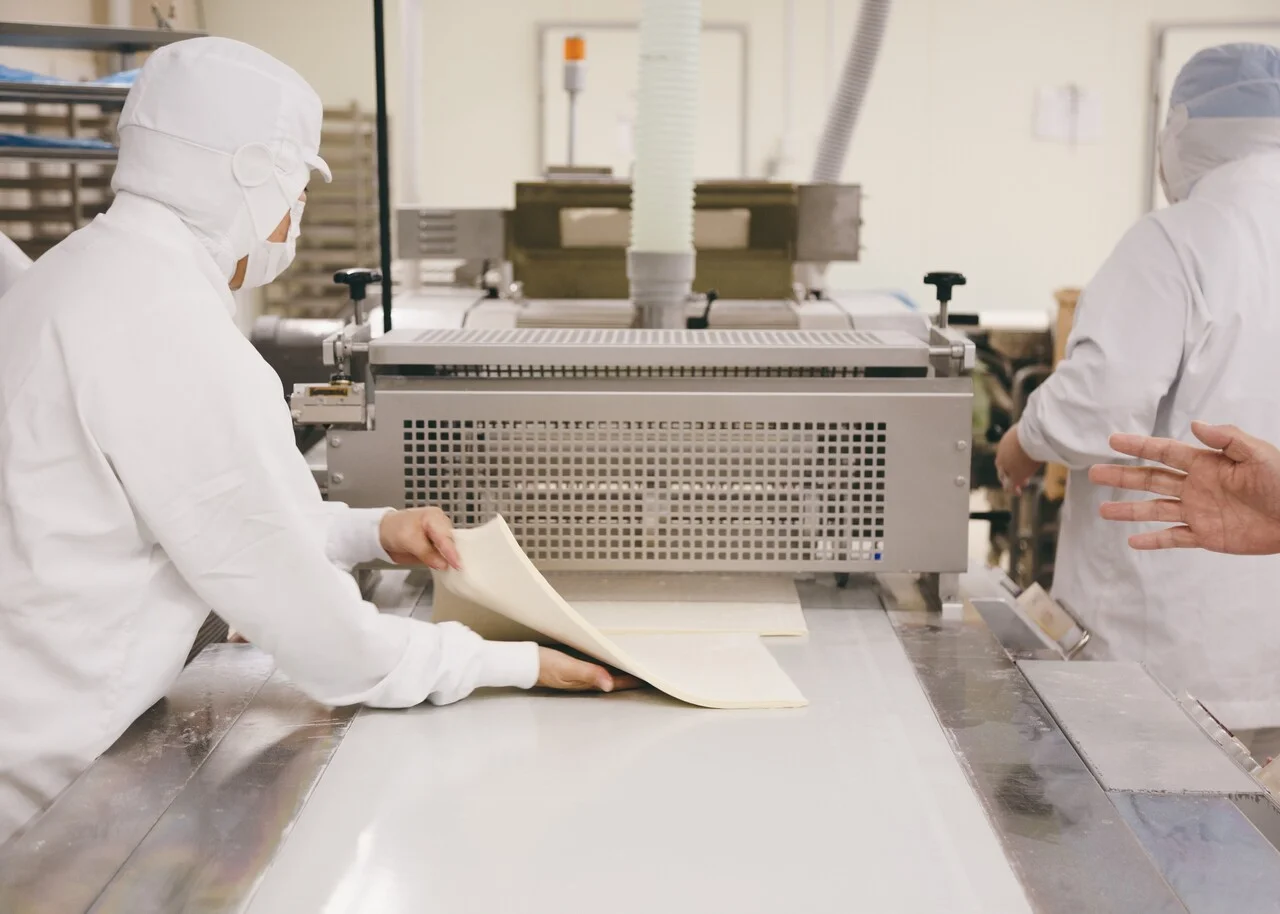
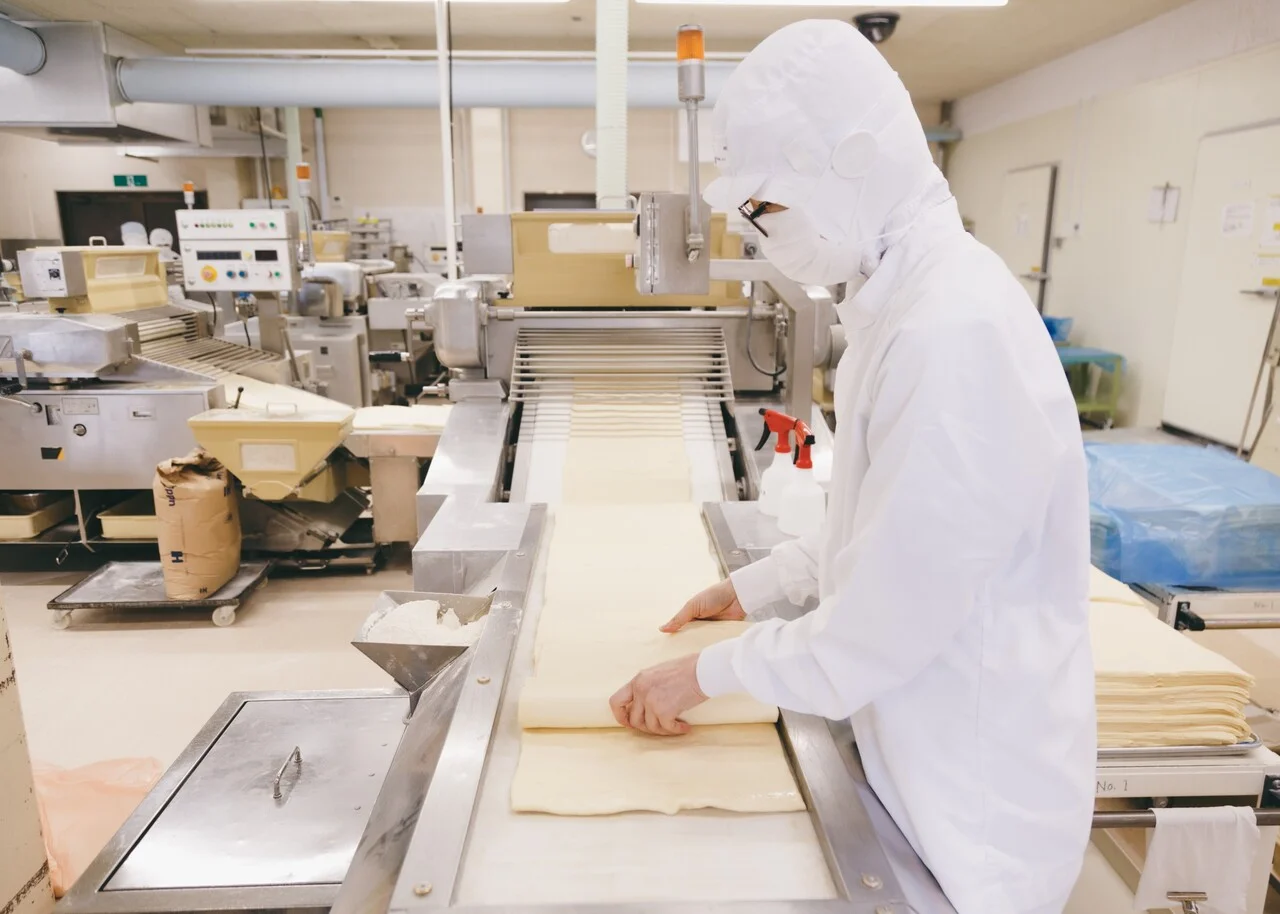
二度の折込を一続きで行うメーカーも多いなか、なぜ敢えてラインを分断するのだろうか?
答えは、パン屋の厨房にある。クロワッサン生地をつくる際、シェフたちは折込を行った後に必ず生地を冷やして休ませる。 温度上昇に伴う生地の緩みの抑制と、油脂の溶け出しを防いで綺麗な層をつくる のがその主な目的だ。 それと全く同じことが、イズムの工場でも行われている。一度目の折込が終わってカットされた生地は、工場内の冷蔵庫へと運ばれ30分?1時間程度冷やされる。ここで生地の状態を整え、二度目の折込へと移されるのだ。
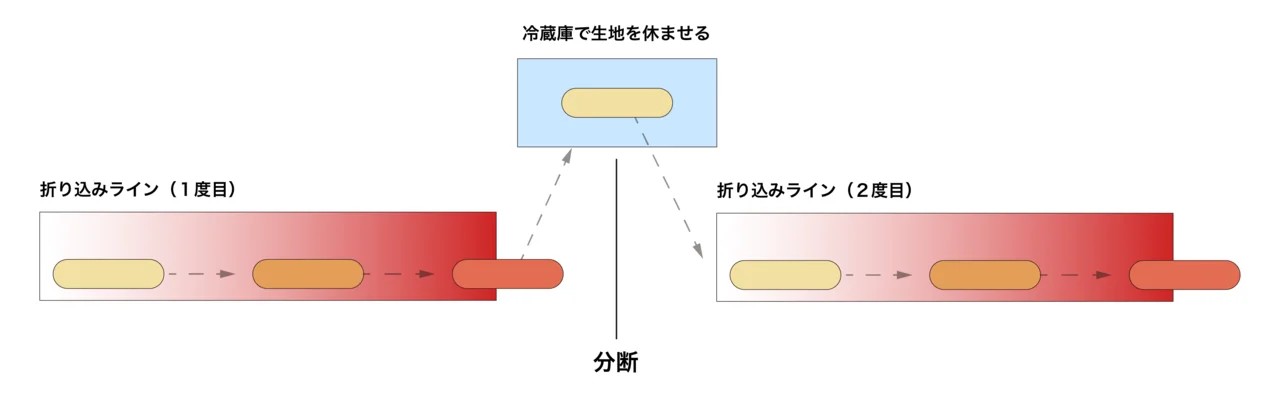
ラインを分断したことによって、必要な人員も、手間も増えた。決して合理的とは言えないが、そこには創業時から脈々と続くイズムのある思いがあった。
田部井「創業時のメンバーは全員が製パン経験者でした。現場を知る人間がつくったからこそ『
クロワッサンをつくるなら折込の後に休ませないとおかしい』
という発想になったんだと思います。
ただ綺麗な層がつくれれば良いというだけなら、工場のライン専用の油脂を使うという選択肢もありました。温度が上がっても溶けにくい特別な性質を持つ油脂で、たしかにそれを使えば層は残るし作業効率も上がります。ですが高温でも溶けにくいということは、人の口のなかに入れても溶けにくいということ。結局のところ、あまり美味しくないんです」
シェフたちのリクエストに応えるためにも、新たな製品開発のためにも、使う原料や製法はできるだけ限定しない。機械都合で美味しさの可能性が狭まるなら人の手で拓く、それがイズムの流儀だ。
もっと自由な表現のために
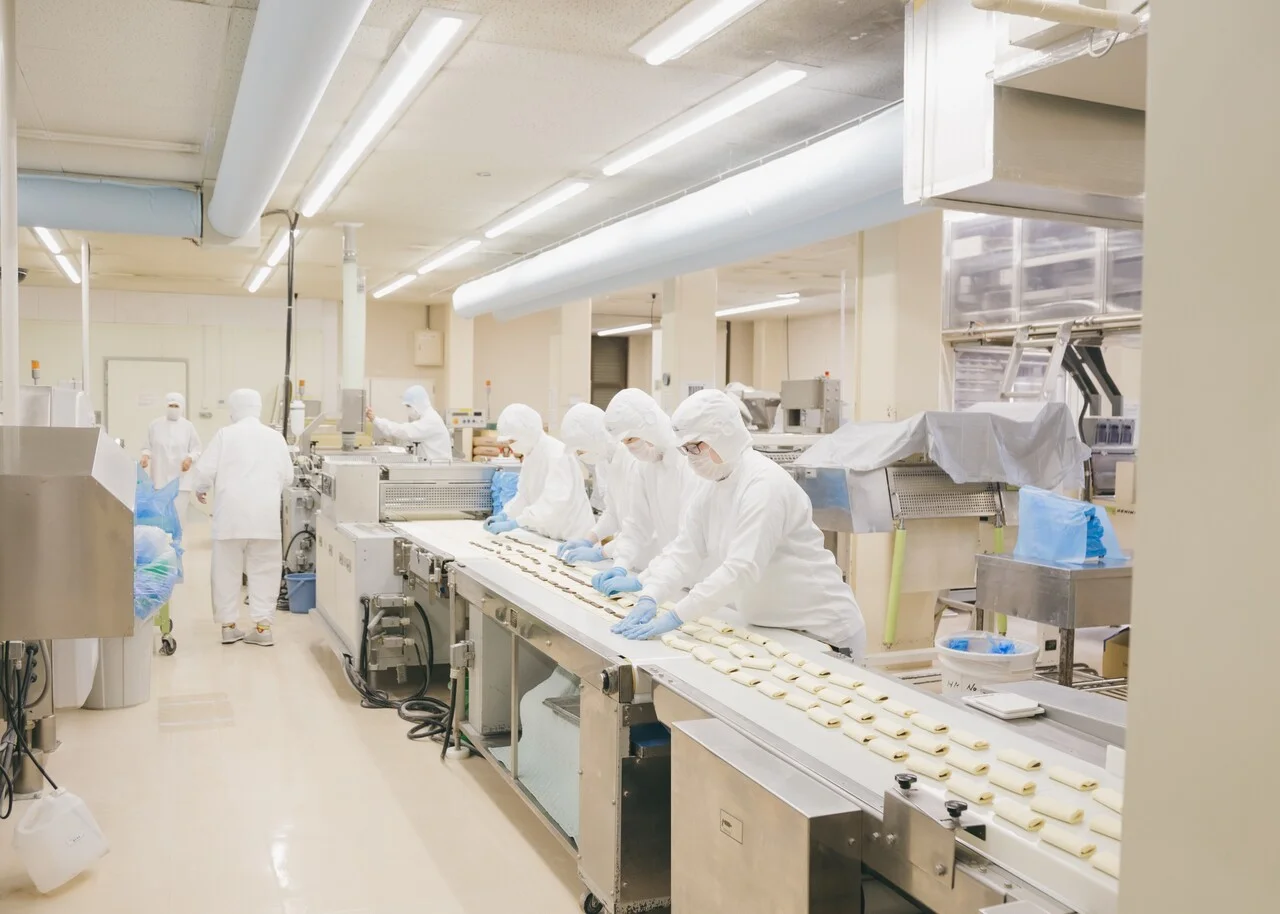
田部井「シェフそれぞれにこだわりってあると思います。できることなら1から100まで、自分で自分の思うようにできたらそれが一番でしょう。ですがただ闇雲に『全部がんばらなきゃ』と思ってしまうと長く続かない。いつかはショートしてしまうかもしれません。
それならば、自分にとってここだけは譲れないというポイントをまず知って、そこに全力を注げる体制をとっていただけたらと思うんです。手をかけたいところに存分に手をかけてもらうために、それ以外のところでは少し肩の力を抜いたって良い。生地づくりというひとつの工程を私たちに任せていただいて、その時間でもっと力を注ぎたい表現や自分の個性と向き合ってもらえたら良いんじゃないかと思います。
シェフたちに安心して任せてもらうためにも、私たちは味と品質にこだわり続けたい。本当にこのやり方しかないのか、もっと美味しくできる方法があるんじゃないかって、これからも考え続けて、チャレンジしていきたいですね」
イズム
〒555-0012 大阪府大阪市西淀川区御幣島6-11-32
HP : https://www.ism-fd.com/